The manufacturing industry is witnessing the entry of automation control systems as a technological attempt to boost the accuracy and performance of industrial processes. This underlines the virtue of industrial automation engineering as one of the most fundamental growth drivers for companies to stay ahead of the curve and achieve long-term profitable growth of their business.
Market Overview of Industrial Automation Engineering
- The market size of industrial automation worldwide reached nearly $175 billion in 2020 and is projected to grow by around 9% until 2025. (Source: Statista)
- The global market size of industrial automation and control systems was valued at USD 172.26 billion in 2022 and is expected to grow at a CAGR of nearly 10.5% in the forecast period between 2023 to 2030. (Source: Grand View Research)
- 60% of all occupations could have 30% of automation activities.
Industrial Automation Engineering: What It Is?
Industrial automation engineering can be defined as a discipline incorporating designing, implementing, and maintaining automated systems in an industrial plant. It employs computers and software for controlling machines and procedures along with designing their architectures. It relies on the involvement of different departments, including chemical, machinery, electronics, electricity, computer, and software engineering. It carries a heavy load in its quality of work, embracing the rapid pace of technological transitions, and reducing the need for manual and mental efforts while improving simultaneous performance.
Most organizations worldwide depend on industrial automation engineers and make use of custom software development services to design and implement systems capable of automating tasks in replacement of manual work previously done by humans. The early adopters of automation engineering techniques have gone through successful results in terms of making their internal business processes more efficient, reliable, and cost-effectively productive.
Types of Industrial Automation Enginerring System for Smart Manufaturing
1. Fixed Automation
Fixed or hard automation generally carries out a single task or process and so is an ideal recommendation for repetitive and well-defined tasks. This type of automation system generally involves a process dictated by programmed commands and is mostly used in manufacturing settings with equipment set for particular functions and unchangeable operations.
To say otherwise, fixed automation is used in manufacturing settings where the use of equipment is fixed for particular functions and there are virtually no changes expected in the operations. As it turns out, accommodating changes in a product design in a fixed automation process is difficult. Benefits of the system include low unit cost and high production rates, whereas inflexibility in accommodating product variety, obsolescence, and being prone to technical fallibility are some of its downsides.
2. Programmable Automation
This type of automation system finds its application when there is a requirement for manufacturing products in batches. It is designed to alter the sequence of operations or facilitate changeable operation sequences and machine configuration by applying electronic controls throughout the manufacturing process. To control the operation, a set of programmed instructions, readable and interpretable by the system is applied. Also required in this form of automation system is a non-trivial programming effort when it comes to reprograming sequence and machine operations.
Remember that the system results in greater productivity in the long run due to being a less expensive automation solution in medium-to-high product volume settings. It is also cost-effectively viable in mass production settings, such as steel rolling mills and paper mills. These systems are flexible, suitable for batch production, and can deal with design variations. However, they yield a lower production rate compared to the fixed automation system and usually involve high investment in general-purpose equipment.
3. Flexible Automation
The utilization of a flexible automation system is mostly noted in computer-controlled flexible manufacturing systems, resulting in rapid and smooth transitions in products and processes. Implementation of a flexible automation system where the product varies more often than not involves human operators, who instruct the computer in coded commands to identify products and their location in the system’s sequence to prompt automatic micro-level changes.
The instructions given by the operator trigger the machine to acquire the necessary tools and equipment to execute the production. Flexible automation systems are used in situations involving batch processes and job shops with high product varieties and low-to-medium job volume. A flexible automation system enables companies to produce a variable mixture of products, offer a medium production rate, and are flexible to deal with product design variation. However, it also requires heavy investment and results in high unit costs compared to fixed automation systems.
4. Integrated Automation
Integrated automation systems consist of two or more types of automation or involve a set of independent machines, processes, and data working in sync with the command of an individual control system. The custom solution created by the system is used to manage and streamline the application of tools and processes to drive better results without involving much human effort. Also, the integrated automation system is used in complex manufacturing settings requiring coordination of multiple processes, and in large factories with expensive machines to improve productivity.
In this form of system, a common database can be used to integrate a business system, supporting the full integration of management operations and processes. Application of this system should be determined based on your business’ labor conditions, competitive pressure, and work requirements, as well as the cost of labor.
Also Read: AI in Manufacturing
Top 8 Benefits of Industrial Automation Engineering
- Better Productivity: Industrial automation solutions have resulted in continuous mass production today, enabling the manufacturing industry to run 24/7 with nominal downtime.
- Optimized Costs: One of the most important upsides of implementing industrial automation solutions is driving a substantial reduction in costs. Emerging technological advancements in robotics, smart machinery, and AI systems have largely attributed to significantly reducing production costs, helping the manufacturing industry enhance the value of business assets and push forward toward more profitable growth.
- Improved Quality: By eliminating human errors and driving greater consistency leading to improved quality of the products, the automation solution is vindicating its viability and efficacy for industrial application. Some tasks that are humanly impossible to be done perfectly can be achieved through automation, including the creation of more complex items, such as electronic goods and pharmaceuticals.
- Reliable Safety: Industrial automation solutions carry the efficacy of improving workplace safety and employee protection, along with reducing human errors and deploying robots and machines to lead reduction in workplace accidents and injuries.
- Better Flexibility: Automation solutions drive more flexibility to the industrial processes and machinery, thereby allowing businesses to adapt strongly to the evolving market demands.
- More Added Value: Automation results in added value by relieving employees of working on mundane and repetitive tasks, thus allowing them to focus on more creative-demanding tasks.
- Enhanced Data Support: Automation allows for automated data collection, particularly during The Fourth Industrial Revolution (or Industry 4.0). With real-time collection and analysis of segmented data, it allows companies to experience enhanced data support and improved product traceability, and to continuously optimize work processes.
- Real-time Monitoring and Maintenance: Industrial automation systems pave real-time monitoring of all the key functions using highly sensitive sensors in cutting-edge industrial machinery to detect and address issues and errors in production processes.
Boost manufacturing efficiency with tailored automation solutions. Connect with experts to optimize your processes today!

Potential of Industrial Automation Engineering for Maximizing Manufacturing Business: 4 Key Tips
If you are planning to introduce automation solutions to your business, one of the most crucial things to follow is to deploy the right team to help you walk through opportunities and navigate the challenges that come with them. Here is a quick rundown on leveraging the team of automation specialists.
1. A Solution Roadmap To The Problems
Before using an automation solution, make a list of the problems you want to solve. This means having a clear vision of your goals and objectives since the initial phase of automating anything, to develop an effective solution. Assistance from an industrial automation engineer will be crucial in spotting the loopholes in your existing processes and their relative impacts on your business. This way, you will get a solution roadmap from the engineer to the problems you want to solve through automation.
2. A Rundown On The Business Case
Once you have understood the areas for improvement, the automation engineer will help you understand the prospective advantages you will gain by implementing automation solutions in the processes. Benefits like decreased labor costs, profitable growth, and quality control are some pointers to consider when it comes to evaluating the business case for automation.
3. Assistance With The Right Technology
When it comes to choosing the right technology, the options are very, ranging from programmable logic controllers to industrial robots and data handling. Since you don’t want to court problems in choosing the unwanted technology for automating processes, it makes sense to pay heed to the automation engineer, helping you choose the right technology best suited to your business needs.
4. Implement The Solution
After choosing the right technology, work with the team of automation specialists to get the most out of your invested money. The experience and expertise of the engineers will come in handy for you to be able to implement automation solutions to smoothen the process and maximize the benefits.
Ready to optimize your manufacturing? Reach out to us for tailored software solutions to streamline your processes and increase operational efficiency.
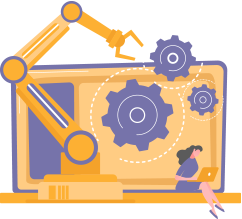
Conclusion
The automation control system witnessed by the manufacturing industry is a technological attempt to increase the accuracy and performance of industrial processes, drive improved quality, productivity, and optimized costs for businesses. Companies looking to automate processes are advised to work with a team of experienced automation specialists. This will result in working with experts to understand various stages of implementation strategies for an effective automation solution. Work with an experienced company offering manufacturing custom software solutions to help you automate entire business processes for greater performance efficiency.